The computer control system of the milling machine is the “brain” of modern milling machines, mainly composed of the following core control components:
Main Control Unit (MCU/ECU):
Central processing unit module (such as Siemens S7 series PLC)
Data storage module (storing construction parameters and fault codes)
Input/output interface module (connecting various sensors)
Human computer interaction interface:
Color touch screen display (7-12 inches)
Multi functional operation keyboard (with waterproof design)
Status indicator panel
Sensor system:
Milling depth sensor group (ultrasonic+laser redundant design)
Three dimensional tilt sensor (X/Y/Z three-axis detection)
Speed sensor (milling drum, walking system)
Temperature sensor group (hydraulic oil, engine, bearings, etc.)
Execution control module:
Hydraulic proportional valve controller
Engine ECU communication interface
Walking speed control unit
Positioning and measurement system:
GNSS positioning module (supporting RTK high-precision positioning)
Laser receiver interface
Ultrasonic Range Finder
Data communication system:
CAN bus communication module
4G/5G remote communication terminal
WIFI/Bluetooth local communication module
Security protection system:
Emergency stop control circuit
Overload protection module
Tilt alarm device
Auxiliary function module:
Automatic lubrication control unit
Spray system controller
Lighting system control
These computer control components are interconnected through an industrial grade CAN bus network to form a complete digital control system, which can achieve:
Precise control of milling depth (± 1mm accuracy)
Automatic slope control
Intelligent adjustment of construction parameters
fault self-diagnosis
Construction data recording and analysis
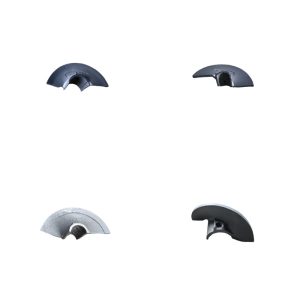
Spiral feeding blade
Basic version: 60Mn, 65Mn high carbon steel (hardness HRC45-50). Wear resistant version: alloy steel+tungsten carbide coating (hardness HRC55-60). Size: Diameter: usually 200~400mm (matching paver model).