- The function of shock absorbers
Reduce vibration transmission: isolate the high-frequency vibration of the roller vibration wheel, avoid vibration transmission to the body or cab, and protect the equipment structure and electronic components.
Improve operational comfort: reduce the vibration and noise experienced by the driver, and minimize fatigue.
Extend equipment lifespan: Reduce the impact of vibration on components such as the body, bearings, and hydraulic system, and minimize wear and tear. - Common types
Roller dampers can be divided into the following categories based on their design and working principles:
(1) Rubber shock absorber
Material: Made of high elasticity rubber or polyurethane.
Features: Simple structure, low cost, corrosion resistance, but prone to aging after long-term use.
Application: Small rollers or low-frequency vibration scenarios. - Installation location
Between the vibration wheel and the frame: isolate the high-frequency vibration of the vibration wheel.
Cab base: reduces vibration transmitted to the operator.
Engine bracket: reduces the impact of engine vibration on the fuselage. - Key selection points
Load capacity: It is necessary to match the weight and vibration intensity of the roller.
Frequency range: Choose the appropriate type based on the vibration frequency (such as selecting hydraulic shock absorbers for high-frequency vibration).
Environmental adaptability: Consider temperature, humidity, and corrosiveness (such as salt spray resistant materials required for seaside operations).
Maintenance cost: Rubber parts need to be replaced regularly, and hydraulic shock absorbers need to be checked for sealing. - Maintenance and troubleshooting
Regular inspection: Observe whether the shock absorber has cracks, oil leakage (hydraulic type) or deformation.
Cleaning and maintenance: Remove surface dirt and oil stains to prevent rubber aging.
Replacement standard: If the shock absorption effect significantly decreases or there is abnormal noise, it should be replaced in a timely manner.
Common faults:
Rubber aging: manifested as cracking and hardening.
Hydraulic leakage: The damping force has decreased, and it is necessary to replace the seal or the whole.
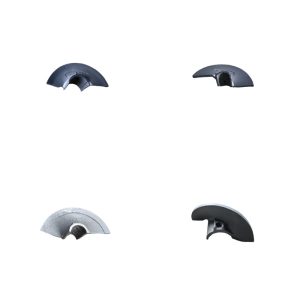
Lame d'alimentation en spirale
Basic version: 60Mn, 65Mn high carbon steel (hardness HRC45-50). Wear resistant version: alloy steel+tungsten carbide coating (hardness HRC55-60). Size: Diameter: usually 200~400mm (matching paver model).